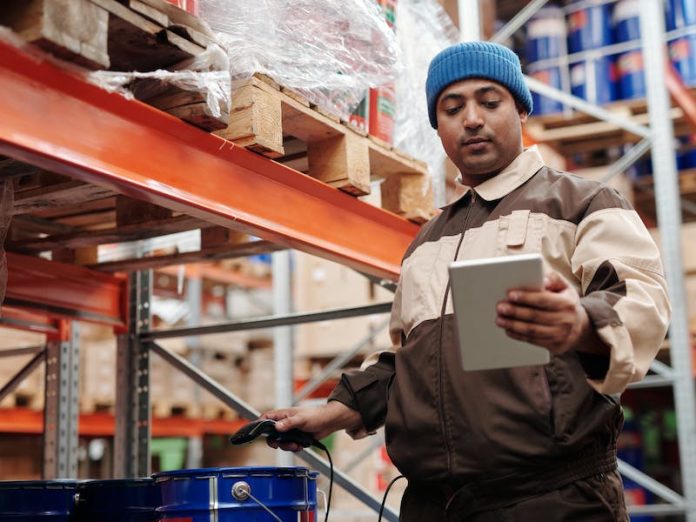
Effectively managing and monitoring temperature-sensitive and perishable items is vital to cold chain processes. Without a well-planned cold chain strategy, you risk wasting products and resources, which can significantly impact your bottom line.
Cold chain management requires a delicate balance to ensure all products are stored, packaged, and transported according to each item’s temperature needs. Thankfully, with advances in technology, the cold chain logistics market has grown significantly, providing businesses with the solutions they need to more effectively monitor and ship perishable goods.
What is Cold Chain Management and Why Is It Important?
Cold chain logistics and management is a process responsible for ensuring safe storage and transport of temperature-sensitive products, such as chemicals, pharmaceuticals, seafood, meat, beverages, and more. This management system is essential as it ensures quality and integrity throughout the supply chain so products are kept safe from spoilage, degradation, and contamination.
If temperatures are not properly maintained or if products are not packaged properly, it not only leads to wasted products, which can cost your business money, but it can also put customers who receive the damaged goods at risk. For example, pharmaceutical products can degrade and become less effective, which can put a patient’s health at risk and if food products spoil, it can lead to the spread of foodborne illness.
Cold chain management is also crucial to ensure your company remains compliant with federal safety standards. Failure to comply with these regulations can result in liability issues, costly fines, product recalls, and reputational damage. If failing to maintain safety standards becomes a recurring issue, it could even result in a temporary shutdown or your business license could get suspended.
Evaluating Your Cold Chain Processes
The first step in improving cold chain management is to audit or evaluate your existing cold chain. You must assess the current state of your operations to identify inefficiencies and where things need improvement.
This starts with taking stock of all of your inventory and making sure you thoroughly understand how certain products need to be stored, packaged, processed, and shipped to ensure compliance with safety regulations. Next, you’ll want to evaluate how your products get from one point to another. This will help you identify who and what processes are involved in the journey of the product so you can determine if there are any gaps or inefficiencies that need addressing.
Records and data are other important factors to review. Are accurate records being kept? Is the data well organized and easily shared with and accessible to the right team members? A major part of cold chain management is efficient monitoring and tracking of records and data pertaining to your products.
You should also assess your cold chain storage, equipment, and devices. Can your storage accommodate your peak stock levels? Are products organized and arranged properly to allow for adequate flow of cool air? Do your devices accurately monitor and display temperatures? If your storage and equipment are not adequate then you may need to upgrade to new equipment and change your strategy for how things are stored and monitored.
5 Best Practices for More Efficient Cold Chain Management
At the end of the day, the best way to optimize cold chain management is to adopt integrated approaches using the latest technologies. By adopting these advanced systems, you can prevent products from going to waste or spoiling, boost cost savings, and improve overall operational efficiency.
1. Implement Temperature Monitoring Systems
When you are dealing with temperature-sensitive goods, having robust temperature monitoring systems is perhaps the most important part of cold chain management. Whether you are dealing with chemical storage, pharmaceuticals, or food, maintaining a stable temperature is vital.
For example, simply keeping all items cold might not be sufficient enough. Some materials in chemicals can separate, for example, if they are kept too cold. Thus, each item needs to be stored at a very specific temperature, and those temperatures need to be regularly controlled and monitored to ensure the product has not spoiled or become unstable.
2. Utilize Appropriate Packaging and Insulation
How products are packaged, both in storage and during transport is also essential to ensuring integrity and quality. When it comes to cold chain products, packaging isn’t just about appearance and how well it appeals to the customer, it is also about ensuring the safety and quality of the product.
If products are not packaged properly, temperature fluctuations during transport can result in spoiling and degradation. Thus, it is necessary to ensure investment in quality packaging and insulation materials as a best practice for cold chain management.
3. Adopt Automated Inventory Controls
With cold chain management, keeping track of inventory is even more crucial as the products on your shelves in storage could spoil if they are not shipped and used by a certain time. Thus, adopting automated inventory controls can be extremely beneficial for product shelf-life management.
An automated system such as this will not only help you keep better track of the products you have and when you need to order more, but it will also help you better monitor the shelf life of those products to ensure they are not going to waste.
4. Optimize Transportation With IoT
Maintaining the optimal temperature of products in storage is one thing, but ensuring those products remain at a stable temperature throughout the transport process is another challenge altogether. Using refrigerated vehicles and ensuring products are packaged and loaded properly is important, but using IoT sensors to continually monitor temperatures during shipment is also necessary.
With IoT, not only can you streamline and connect all of your cold chain processes, but you can also get real-time updates on products that are actively in transport. This enables you to monitor temperatures throughout the entire journey of the product. IoT sensors can also send real-time alerts to let you know if any temperature is dropping below or going above safe levels, which allows you to take necessary actions right away to resolve the issue before it’s too late.
5. Adopt Telematics Platforms
Utilizing technologies like IoT and temperature monitoring systems won’t matter if you don’t have a good program for receiving and visualizing all that data. Telematics visibility platforms enable you to receive, visualize, and analyze the data from your tracking and monitoring devices all in one place. These platforms allow you to transform the data you receive into meaningful insights so you can make more effective decisions.
As a whole, visibility platforms can help with:
- Real-time data visualization
- Cost reduction
- Risk mitigation
- Scalability
- Quality and safety compliance
Visibility platforms also ensure everyone on your team can easily access and share the same information, which can improve collaboration and communication. When all of your data is easily accessible in one place, it ensures everyone is on the same page and working together effectively.
Wrapping Up
If your company is struggling with cold chain management, integrated technologies can significantly improve your efficiencies and help you save money. Embracing the best practices listed above can help you streamline your processes and ensure that your products maintain a stable condition all while keeping you compliant with safety regulations. This is also important if you want to grow your business in the future and avoid liability issues or damaging your company’s reputation.
About the Author
Indiana Lee is a writer, reader, and jigsaw puzzle enthusiast from the Pacific Northwest. An expert on business operations, leadership, marketing, and lifestyle, you can connect with her on LinkedIn.